Solder Copper Pipe Fittings with HGW Tin 97
- Tony, the Welder
- Nov 1, 2021
- 2 min read
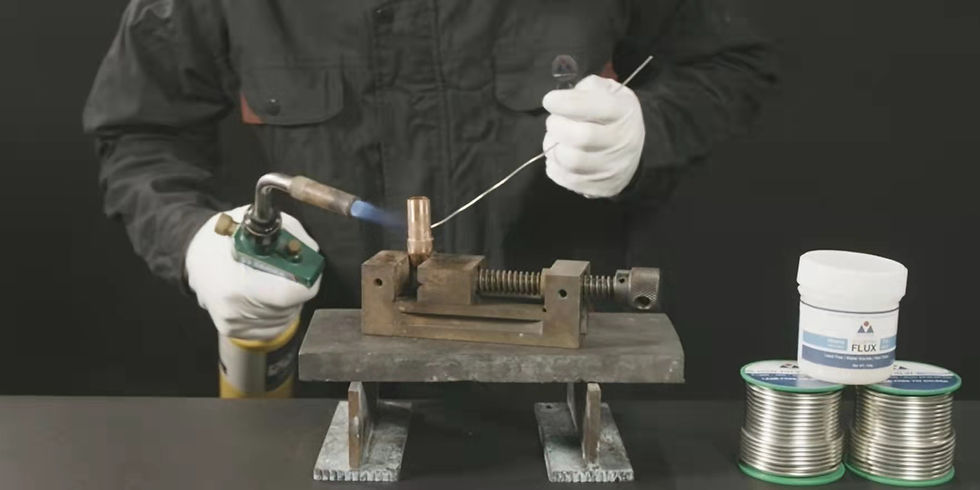
As a typical soldering material, the Sn-Pb alloys are widely used in the electronic and plumbing industries due to their excellent properties. However, in recent years, many countries have introduced relevant regulations and ban on toxic and hazardous substances. As a result, lead-free has become an inevitable trend on developing solder products. Therefore,Sn-Ag, Sn-Ag-Cu, and Sn-Cu alloys are the most commonly used lead-free solders, currently.
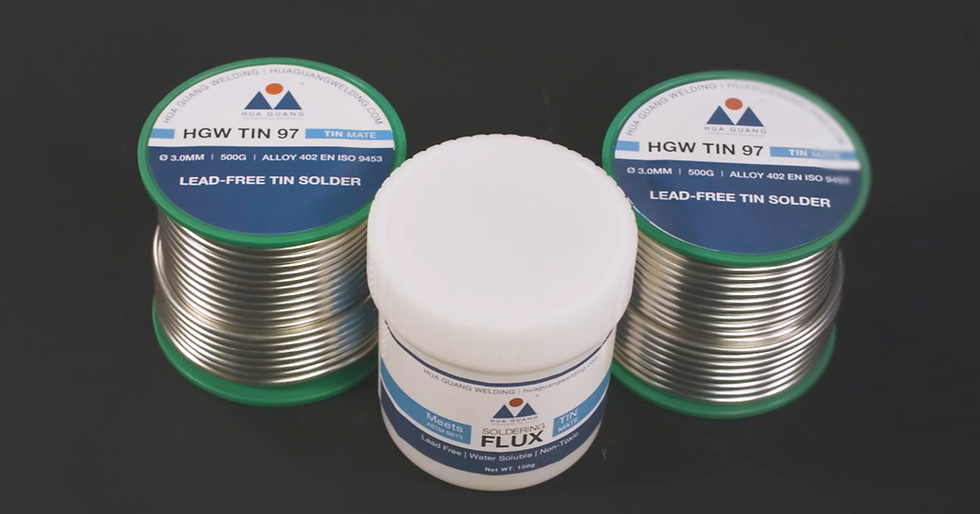
Hua Guang has launched Tin Mate series of Sn-Cu solders. Take HGW Tin 97 as an example, as it does not contain any precious metals, the price is quite economical. At the same time, it has excellent liquidity and wide applicability. It is compatible with usually applied soldering processes such as torch soldering and electric iron soldering. Flux-cored solder wires are commonly used in the electrical industry, while solid solder wires are suitable for the plumbing industry. The specific product introduced here is the solid version.
HGW Tin 97 is lead-free. It has a low melting temperature, and well-resistance to oxidation, making it as a suitable choice for soldering copper pipes and copper fittings in drinking water systems.
In order to ensure the quality of soldering joints, chemical or mechanical methods can be used to clean the base metals before soldering, especially at the soldering area. After then, the cleaned parts should be soldered on time to prevent the surface to be contaminated or oxidized again.

Suitable gap width is essential for soldering compactness and joint strength. Due to the excellent fluidity of Sn-Cu alloys, the assembly gap can be as small as possible, but uniform. When lapping, attention shall also be paid to the lap length between the base metals, which is usually kept as 4 - 5 t ( thickness of the thinner part of base metals), and blind hole should be avoided when socketing.

During pipe fitting soldering, proper preheating is needed. Scratch the joints lightly to avoid local overheating the base metals. For horizontal joints, it is more tricky to wet and fill the joint properly, as gravity may prevent the solder from flowing to desired spots. To get around this issue, we heat the tube from the bottom, and then fill the gap around the joint using the tip of the solder wire. Finally, molten Tin 97 solder wets the base metal, fills the gap, dissolves and diffuses to the base metal under capillary action. Remove the slag and residue immediately after soldering.

At the same time, the components after soldering should be inspected to ensure that they meet the requirements on using, such as, appearance inspection, metallographic observation and microstructure analysis of each soldered joint. A qualified joint should be ensured, there are no defects such as inclusions, pores, cracks, incomplete penetration, etc. And it should form a strong enough metallurgical bond with the base metal. Sleeve fittings need to be observed for penetration depth. And if necessary, the tightness and corrosion resistance also should be tested.
Comments