Fundamentals and Applications of Aluminum Brazing
- Tony, the Welder
- May 7, 2020
- 1 min read
Updated: May 18, 2020
The increasing use of aluminum for parts has spawned the development of better aluminum filler metals and fluxes for brazing. All commercial filler metals for brazing of aluminum alloys are aluminum-base alloys themselves. Common aluminum filler metals are based on the aluminum-silicon binary alloy system and contain silicon as the melting-point depressant with or without additions of zinc, copper, and magnesium. Lower melting points, greater fluidity, higher wettability and better joint filling performance could be attained with some sacrifice in resistance to corrosion, by adding copper and zinc. And the additional magnesium is used as an oxygen getter to improve brazing.
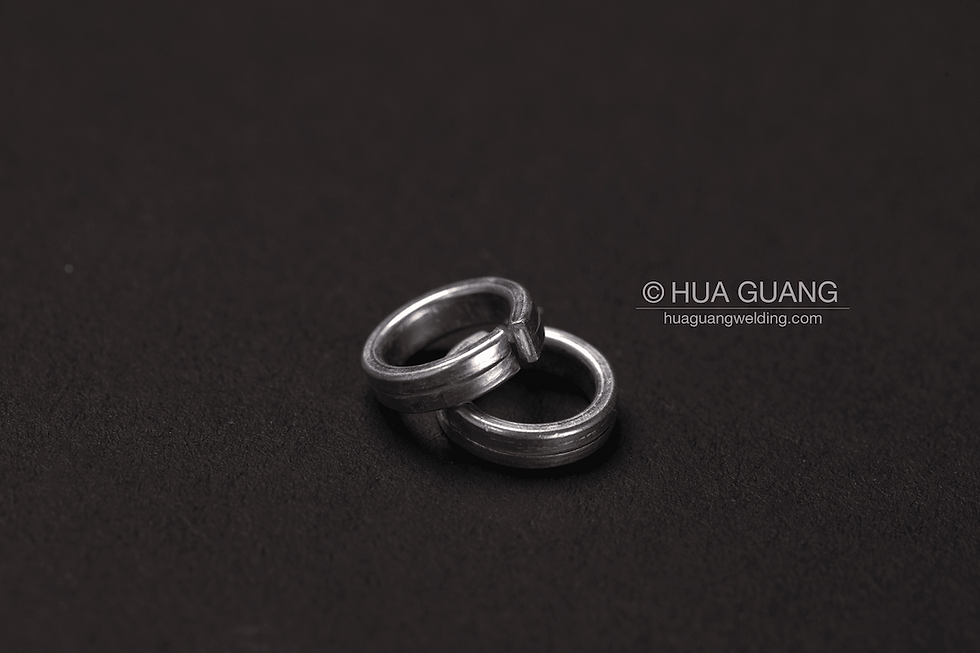
Most of brazing filler metals in the BAlSi classification are general purpose brazing filler metals and are typically used in heat-exchanger and condenser applications (radiator, air conditioning condenser, air conditioning evaporator, add-on
transmission oil cooler, etc.) to join fins or pipes made by the following grades of aluminum and aluminum alloys: 1060, 1035, 1100, 3003, 3005, 5005, 6061, 7005, and casting alloys 710,711 and 850.0 by the torch, dip, induction or furnace brazing process in air or controlled atmosphere, including vacuum.

Fluxing is essential for all processes, except when brazing aluminium in a vacuum. When brazing copper, nickel is usually plated on the copper surface to reduce the effect of brittle compounds between aluminum and copper. Particular care also has to be taken to maintain the required temperature range for brazing.
😃